“Very few sheet metal fabrication places do what HUI can do—from a whole scope of things.”
—Tim Littlefield, Cranial Technologies Device President
Having a baby is exciting! We work so hard preparing ourselves—baby-proofing the house, stocking up on supplies and choosing outfits. Unfortunately, we cannot prepare for everything. Plagiocephaly, better known as “flat head syndrome,” is a condition that afflicts nearly 47 percent of infants. How do we treat something as common as this? That’s where Cranial Technologies comes in.
The Situation
Cranial Technologies, located in Arizona, specializes in the diagnosis and treatment of plagiocephaly. The imaging system used for this has five mounted cameras that take pictures from every angle of an infant’s head, including an overhead shot.
Ever conscious of technological improvements, Cranial Technologies employed a local industrial designer to redesign their product to accommodate for these advancements. However, when it came time for manufacturing, the manufacturing and tooling quote did not meet Cranial Technologies’ specified requirements. In fact, Cranial Technologies would have needed to outsource and manage the project overseas—a costly and inconvenient endeavor. Fortunately, a former HUI employee who happened to be familiar with Cranial Technologies recommended HUI—thus, a working relationship was born.
The Problem
The design Cranial Technologies presented to HUI was made almost entirely of plastic, which called for expensive tooling up front. Plus, the design was complicated and required multiple people to assemble. So, the design needed to achieve these three main goals:
- Lower costs
- Single person assembly
- Complete isolation between the camera mounts and the walking platform
The Obstacles
Plastic and aluminum were the main materials used for the original design, resulting in elevated tooling and material costs.
- With the choice to redesign this product with sheet metal, which is more cost effective, new obstacles arose in translating the original industrial designs for sheet metal purposes.
- Engineers experienced difficulties with the three-inch platform height restriction
- The original product had large, heavy parts, so it was difficult to assemble
- Establishing the correct moment of inertia and mount the tower with enough support to keep the top camera stable.
It is relevant to note that the distance from Arizona to Wisconsin seemed a bit harrowing at first; however, any concerns that may have worried Cranial Technologies’ Device President, Tim Littlefield were immediately assuaged by HUI’s evident competency and willingness to help. Upon their first in-person contact, HUI was highly responsive to Cranial Technologies’ needs. Naturally, HUI and Cranial Technologies maintained open lines of communications, building trust between two companies separated by nearly 2000 miles.
The Solution
From the conceptual stage throughout the duration of the project, HUI was upfront and honest about design and engineering complications and pricing. “It made the decisions easier,” said Littlefield.
The cost of the product was addressed first and easily accommodated by substituting sheet metal for plastic and aluminum. To combat the challenges of converting a plastic design into sheet metal, HUI engineers created a sheet metal design with an octagonal platform to show that this product could maintain its aesthetics while remaining cost effective. Therefore, HUI was able to redesign a product of a similar layout and reduce the unit price by 60.4 percent through design changes like fabricated sheet metal shrouding and weldments, substituting the aluminum platform for plywood, implementing tighter simulated bend radiuses and eliminating tooling, most complex weldments, castings and tubing.
Despite the three-inch platform restriction, HUI engineers were able to work with the obstacle. They also applied cut-outs to the platform, making it completely separate from the surrounding towers, helping to isolate the cameras and minimize vibration.
Using what they learned from that first functional prototype, HUI engineers were able to design for easier assembly by reducing the weight and assembling the tower on the ground and then tipping it into position. The original product had a lot of large pieces to assemble, and numerous types and sizes of fasteners, which contributed to the difficulty of the situation. So, HUI engineers redesigned for smaller pieces to fit together, minimized the amount of different fasteners, and simplified the assembly to the point that one person could build the entire unit.
Leveling pads were installed to help adjust the platform and aid in isolating the cameras. As far as tower rigidity is concerned, HUI engineers needed to match moment inertia of the original design which they were able to simulate and reiterate through SolidWorks analysis, and test with a physical prototype.
The Outcome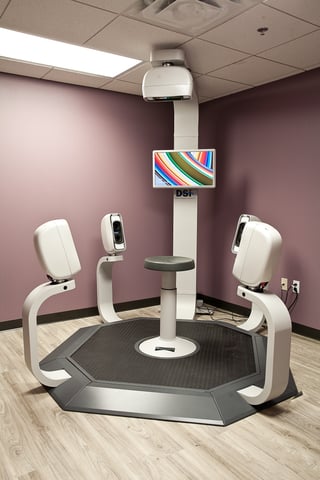
HUI’s second prototype was, as Littlefield would say, “right on the money.” Not only was HUI able to redesign a more economical product that could be successfully assembled by one person with complete isolation between the camera mounts and the walking platform, but they also did so while maintaining lead times. This new, improved product enabled usability through an open layout and eliminated tripping hazards.
Overall Savings:
- HUI reduced the per unit cost by 60.4 percent
- The simplified design reduced tooling costs by 83.3 percent
- Lead time per unit is now four weeks as opposed to the initial 10 to 12 weeks
- Reduced system size by approximately 30 percent (thus similarly cutting down on our space requirements in every clinic)
- Cut back on different fasteners by 85 percent, thus simplifying the install process
- Can now ship in one crate as opposed to four
- Build time cut in half
Testimonials:
"HUI’s ability to gather feedback from the install of the first article, and make adjustments to design for first production units, which came just several weeks later, was impressive! This immediately eliminated a cabling challenge that we identified during the first install.”
—Tim Littlefield, Cranial Technologies Device President
Danielle Larry is an employee of Cranial Technologies Inc. Milwaukee location. As a Baby Imaging Specialist, Danielle has first-had experience with this new imaging system. Here’s what she as to say:
“I have gotten nothing but good responses from parents—
‘Wow, this is cool.’ ‘This is very high-tech.’ The design is great for ease of use, especially with the open side concept. The minimal interruption to camera function with any vibrations or knocks is awesome! And the folks from HUI that came down to help install the machine in Milwaukee were very friendly and knowledgeable!”
—Danielle Larry, Cranial Technologies Baby Imaging Specialist
At HUI, we specialize in custom solutions for our customers. Contact us today with your medical cart designs and questions today!